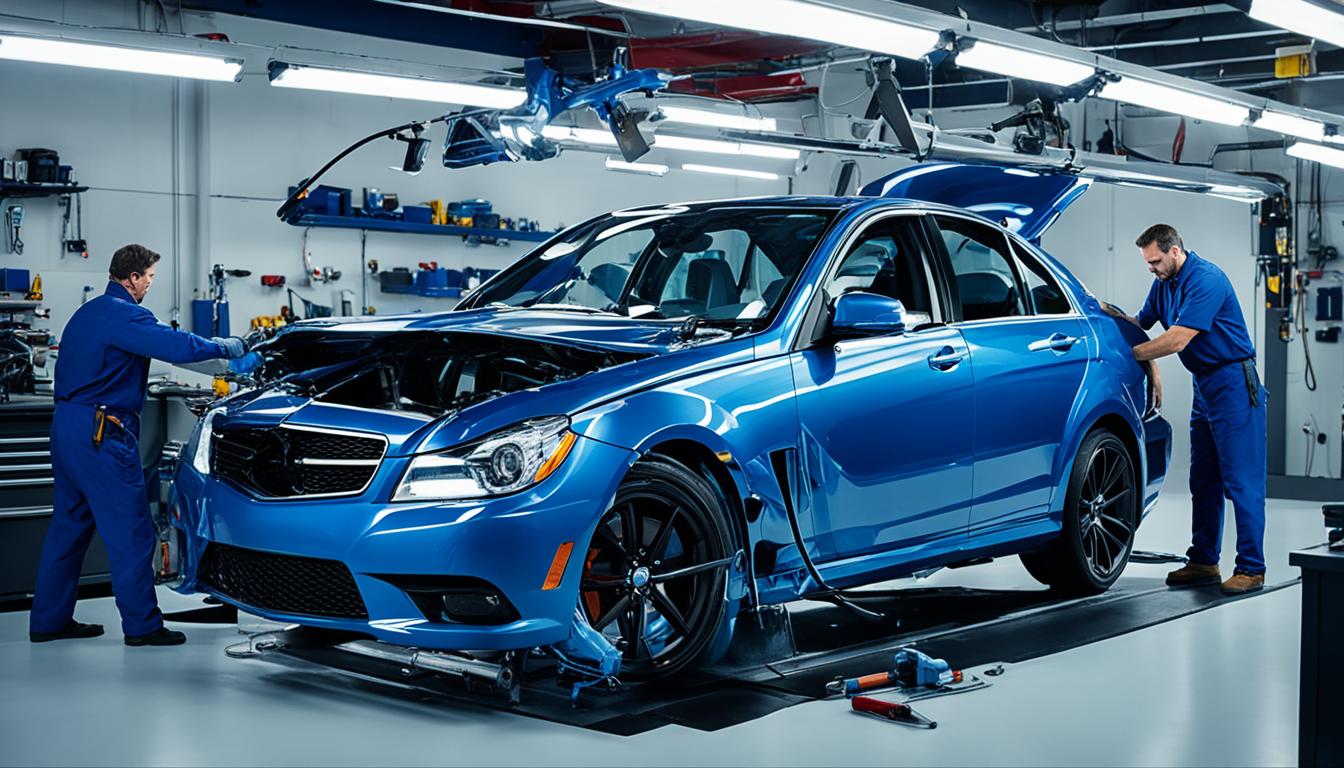
The Benefits of Using OEM Parts for Collision Repair
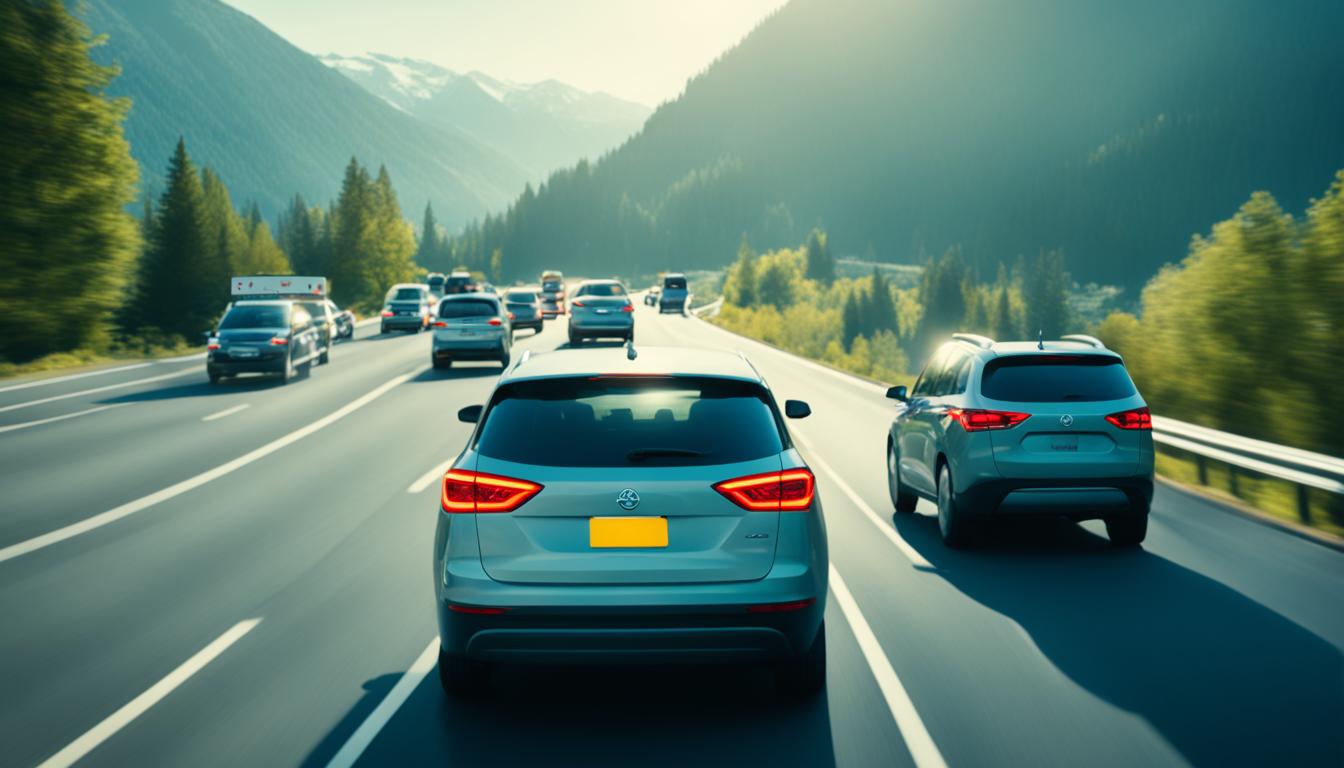
How to Improve Road Safety for Your Fleet Vehicles
Deciding to repair or replace machinery is a big choice. You should think about many things before deciding. Look at the benefits of each option. Also, think about the cost, the machine’s age and shape, how any downtime will affect you, and the impact on the environment. Weighing these factors will help you choose what’s best for you.
Key Takeaways:
- Consider the benefits of repair versus replacement in terms of functionality and performance.
- Evaluate the cost implications for both repair and replacement options, including parts, labor, and downtime.
- Assess the age and condition of the equipment to determine if repair is feasible and cost-effective.
- Take into account the impact of downtime on productivity and operations.
- Consider the energy efficiency and environmental impact of both repair and replacement options.
The Benefits of Repair vs. Replacement
Deciding whether to repair or replace your equipment is crucial. It affects your business’s efficiency and costs. Weighing the benefits of each is important.
Repairing equipment has its perks, especially if you’re a small business or on a tight budget. It’s often cheaper to fix things. This approach lets you use your equipment longer and saves money compared to buying new.
New equipment, though, can make your business more productive. It brings in new tech and features. This can make work smoother and better. Plus, new items tend to need less fixing, which means fewer work stoppages.
Think about your business’s needs when choosing between repair and replacement. Look at how old, how worn, and how well-maintained the equipment is. If it’s fairly new and still in good shape, fixing it might be smart. But, if it’s old and often breaks down, it’s probably better to replace it.
Make your decision by carefully analyzing your situation. Think about the costs, benefits of both options, and how they fit your business needs. This way, you can choose what’s best for now and the future of your business.
Assessing Cost: Repair vs. Replacement
When you’re thinking about fixing or getting new equipment, looking at the costs is very important. You need to check the repair, replacement, and compare all costs. This helps you choose what fits your budget and business best.
Repair cost: Finding the repair cost means looking at a few things. You have to think about the parts’ price, how much it costs to fix, and any time the equipment can’t be used. If the equipment needs a lot of fixing or rare parts, it can be more expensive. And, finding those parts at a good price can also be tough, especially for old equipment.
Replacement cost: Figuring out the cost to replace something is not just about buying new equipment. You also need to think about getting rid of the old one and if you can get money back from it. By adding these costs, you’ll know the real price of replacing the equipment.
To choose wisely, compare the costs for fixing and getting new equipment. Look at everything for repair (parts, labor, and not working time) versus everything for replacement. This clear cost comparison will show the money side of each option.
Just so you know, cost is not the only thing to look at. Think about the equipment’s age and shape, how not working affects you, and any new tech that might save you money. When you consider all these points, you’re more likely to make the best choice for your budget and work.
Take a look at the image below to visualize the cost assessment process:
Evaluating Age and Condition
Thinking about fixing or replacing equipment needs careful thought. It’s key to look at how old and worn the machinery is. If it’s not too old, parts can be saved and fixing it might be cheaper. But sometimes, old and worn out equipment just needs to be swapped for new to work safely and well.
Finding out the maintenance cost percentage (MCP) is a big part of this. The MCP shows if fixing or buying new stuff is smarter. To get the MCP, you divide what you spent on fixing by how much the equipment cost at first, then times it by 100. A high MCP means fixing is getting pricey, so new might be better. But a low MCP shows you can keep fixing it without spending a lot.
Machinery must be checked as it gets older. Regular checks and fixes can stop problems early and make equipment last longer. Also, tracking the MCP helps manage costs and decide when to fix or buy new things.
The Importance of Regular Maintenance
Keeping up with maintenance, like checking, cleaning, and small fixes, is a must. This keeps equipment running well and lasting longer. A little care now can save big repair costs later.
- Regularly check for signs of damage, like rust, loose parts, or strange sounds.
- Have a plan to fix things before they break and stop work.
- Stick to the manual for things like changing filters and fluids on time.
- Teach your team to do small maintenance tasks, so gear stays in good shape longer.
- Keep a record of all the work done on your equipment to watch over costs and how they perform.
By watching your equipment’s age, wear, and upkeep price, you make smart choices about fixing or buying new. Focusing on care and stopping big issues early can extend how long your machinery works well and cut down on surprise costs.
Assessing Downtime Impact
When deciding on equipment maintenance, know that downtime’s effect is key. Downtime can cause big drops in work, affecting how much can be done, how much money is made, and what the customers think. So, it’s important to think hard about how much it would cost if it stops working, including its effect on your work.
Problems needing fixes often mean unplanned downtime. Fixing things may pop up out of nowhere, stopping work. This can lead to less finished work, orders being late, and more money spent because workers can’t do their jobs.
On the other hand, changing the equipment means you can pick when to switch it during times you plan not to work. Doing so can make work smoother and lessen how much work is disrupted. By changing things during breaks, businesses can lower the chances of work coming to a standstill.
It’s vital to look at how important the equipment is to what you do and what will happen if it stops. If losing the equipment for a while would cost a lot, it may be smarter to change it before something major happens. In these cases, the money you save by not having it break would be more than what you’d pay to change it.
Yet, sometimes fixing it to avoid a long shutting down is a sound move. Putting money into repairs to stay working can be a good bet. This way, the work keeps going, big problems are avoided, and the wallet doesn’t take as big of a hit from not working.
Ultimately, deciding to fix or change equipment comes down to looking at how much stopping work would cost and how it affects your job. Thinking over these points helps pick the best decision to keep work going, avoid big stops, and make the job better.
Energy Efficiency and Environmental Impact
Deciding whether to fix or swap your equipment is about more than just the price. It’s smart to think about how much power each choice uses and its impact on the world. Choosing more efficient gear can save you money on your energy bills.
When you pick equipment that uses energy better, you help the planet. This lowers the bad stuff we put in the air and saves money for your company over time.
Updating to new, efficient gear doesn’t just lower your bills. It makes less bad stuff for the planet. Every choice you make for a cleaner world matters a lot.
Mending or changing your equipment calls for a hard think. Going for new gear might seem costly now. But it saves money and does good for the earth in the long run.
The Availability of Parts for Repair
One key thing to look at when deciding to repair or replace is part availability. If itβs hard to get the parts needed for repair, this makes choosing repair tricky. It might be cheaper and faster to just buy new equipment.
Yet, if you can easily find and afford the parts, fixing is a good choice. Easy access to parts means repairs go smoothly and fast. You save time and control how much repair costs.
What’s more, picking repair helps the planet. It means less waste and supports greener practices. This matches the big push for being kinder to our environment everywhere.
Looking at part availability helps you figure out if fixing is doable. If parts are hard to get or cost too much, replacing the equipment could be better. But, when parts are easy to find and don’t break the bank, repair is smart and eco-friendly.
Conclusion
Deciding to repair or replace your equipment is not simple. It involves many important factors. These include the repair costs, how old and worn the equipment is, and how much downtime you can manage. Also, think about energy use, the price of parts, and what is best for your business.
Every case is different. What’s good for one business might not be for another. Look at the benefits and downsides of fixing or buying new. This will help you choose what’s best for you. Talking to specialists or using special software for maintaining equipment can help too.
The main aim is to get the most from your equipment. Also, you want to spend less and have less downtime. By making smart choices and knowing your needs well, you can make the right call. Choose what keeps your equipment running well and helps your business grow.